Navigating Manufacturing’s Incremental Future: Key Findings for Industry Leaders
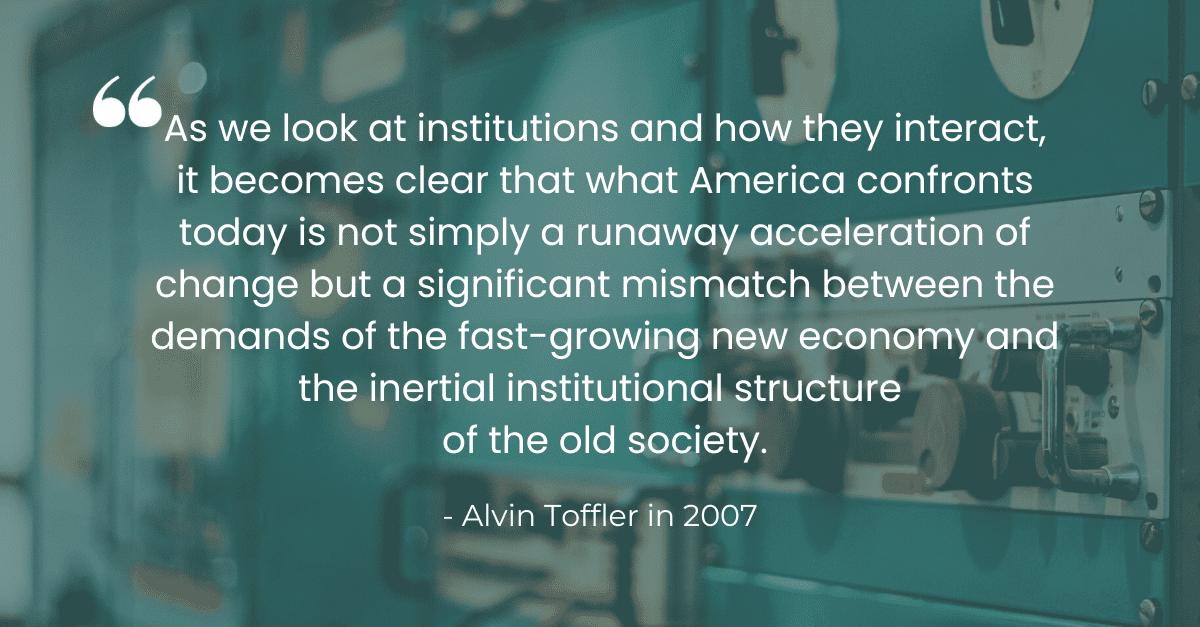
Manufacturing is no stranger to change. From the dawn of mechanization to today’s data-driven automation, producers constantly adapt processes and business models. However, revolution tends to be rare. Evolution is far more common.
In revisiting a manufacturing study we conducted for the Department of Defense, we saw the continued relevance of our findings. We situated our synthesis of over 30 C-suite and manufacturing expert interviews in today’s reality, with meaningful manufacturing legislation now in place and on the heels of the longest UAW strike. We share those findings below.
Change Will Be Rapid Yet Incremental, Not Revolutionary
The manufacturing industry is expected to reach $14.83 trillion this year. With advanced technologies like AI, robotics, and additive manufacturing converging, the prospect of radical shifts looms. But wholesale disruption is unlikely in the foreseeable future.
Additive manufacturing exemplifies the measured pace. This market is projected to grow from $13.1 billion in 2021 to $51 billion by 2030. Impressive growth, but still under 0.5% of total output. Robotics too will expand, from 189 robots per 10,000 U.S. workers today to approximately 300 per 10,000 by 2025 – far below Asian leader South Korea’s 1,000+ per 10,000.
While pioneering companies will shake up models, most will iterate. Change will quicken but remain gradual. Leaders must pilot emerging methods while optimizing legacy systems and easing the transition for the traditional workforce.
Securing Manufacturing’s Future Workforce is Paramount
Accessing skilled labor is the number one challenge facing manufacturers. With over 50% of manufacturing workers above age 45, retaining institutional knowledge is already difficult. Compounding this, over two million manufacturing jobs are projected to go unfilled by 2025. The workforce dimension is critical to manufacturing’s future.
2023 UAW Strike Highlights Workforce Risks
The 2023 United Auto Workers (UAW) strike exemplified ongoing workforce risks. The 6+ week strike against automakers, the longest in UAW history, cost billions in losses and disrupted supply chains.
While the strike ended with wage and job security gains, the unrest signals a tightening job market. Workers’ increasing leverage and demands will only grow. Manufacturers must prioritize workforce investments and foster positive labor relations to avoid disruptions.
Multipronged Approach Needed to Address Skills Gap
Manufacturing’s future hinges on proactively securing human capital. With the right workforce strategies, manufacturers can gain a competitive advantage.
Attracting talent will require revamped recruiting and streamlined hiring. But upskilling existing workers is equally vital. Training programs, mentorships, and on-the-job learning build adaptable talent.
Integrating apprenticeships and applied education will prime the future workforce. Creative compensation catering to younger workers can widen labor pools. Workforce development programs and continuous skills training are critical to optimizing labor utilization.
Virtualization and Specialization Reshape Business Models
Emerging technologies will enable highly specialized and distributed models. Smart manufacturers will coalesce into nimble networks organized around expertise areas. Virtual platforms will allow remote collaboration to meet shifting customer demands.
Additive methods combined with closer designer-user feedback loops will drive small batch production and rapid iteration. Capital spending will migrate from fixed assets toward simulation and digital twin capabilities. Consolidated supply chains will disperse toward democratized, open models.
Asia Reshapes Global Manufacturing but Introduces Risks
China’s manufacturing ascent has been swift. Its production eclipsed the U.S. in 2010, and China now accounts for 30% of global output. However, success makes China pivot from manufacturing taker to maker. With intellectual property theft rampant, the Pentagon sees future conflicts centered on information rather than territory.
Yet dependence persists. As of 2022, 80% of advanced semiconductor fabrication is located in Asia. While the CHIPS Act provides $52 billion to incentivize domestic semiconductor manufacturing, fully reducing reliance will take years. Policymakers must balance pragmatism and security.
Virtualization Multiplies Supply Chain Vulnerabilities
Dispersed suppliers and open collaboration networks create oversight difficulties. With large, multi-tiered supply chains, ensuring integrity is already arduous. Additive manufacturing also heightens IP vulnerabilities given digital file sharing.
Proactive controls are essential. Manufacturers must validate materials, inspect finished products, and implement blockchain ledgers to enhance traceability. Redundant suppliers and regional capacity provide contingency. Cyber war gaming will identify other weak points.
Recent Legislation Seeks to Bolster US Manufacturing
Recognizing supply chain risks and China’s rise, the U.S. government passed major legislation to spur domestic production:
- The bipartisan CHIPS Act provides $52 billion to bolster semiconductor manufacturing. This legislation seeks to reduces reliance on Asian imports.
- The Infrastructure Investment and Jobs Act designates $550 billion to modernize infrastructure like roads, railways, and broadband. This facilitates commerce.
- The Inflation Reduction Act offers $370 billion for energy and climate investments. Incentives for renewables and electrification can benefit green manufacturers and help traditional manufacturers transition to a greener future.
These represent government efforts to catalyze manufacturing investments, improve competitiveness, and enhance resilience. Proactive leaders should tap into these opportunities.
Key Actions for Manufacturing Leaders
Optimizing for this evolutionary era involves concrete steps manufacturers can undertake today:
- Take steps now to strengthen labor relations to avoid costly disruptions down the road.
- Pilot flexible resourcing models tapping niche experts as-needed to enable agility.
- Redesign work around human-machine collaboration to address the skills gap.
- Institute continuous learning programs to develop adaptable talent.
- Validate materials, implement blockchain, and enhance oversight to secure supply chains.
- Diversify sourcing options with redundant capacity to mitigate disruptions.
- Run scenarios exploring trade conflicts, cyber-attacks, and other threats to identify vulnerabilities.
- Seek production efficiencies and sustainability gains from new legislation.
While the trajectory is incremental, changes will compound quickly. Manufacturers must become learning organizations adept at navigating uncertainty. But investing now in workforce, technology and supply chain resilience will ensure competitive strength for the future.
- Categories
- Futures and Foresight
- Workforce of the Future